Sand moulding is a critical first step in our hardware manufacturing process. Moist sand is packed tightly and precisely to make two-part moulds. The texture of the sand is transferred to the metal, and the result is a typical pitted texture, ideal for chiseling, or left as is for our Wabi-Sabi texture.
Craftsmanship
Moulding
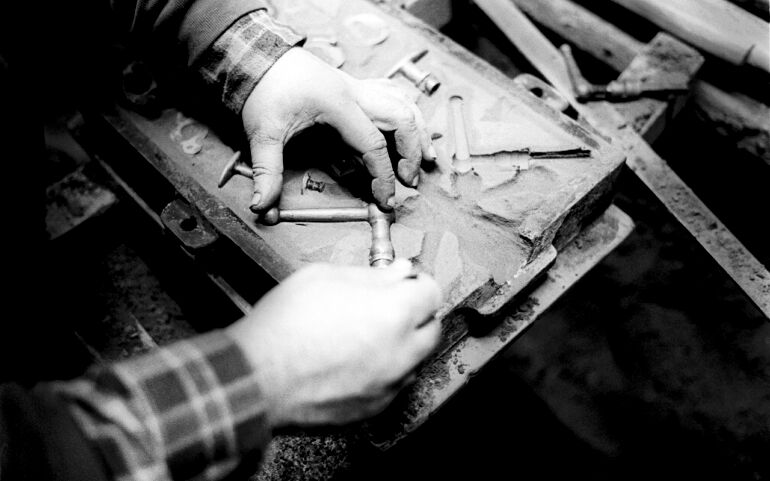
Casting
The sand moulds go into an oven to harden the sand to make it ready to accept the casting. Brass gets melted in a crucible at approximately 1000°C (1320°F) after which it is poured into the moulds.
Filing
Hand cast pieces end up with a hard-surface crust which needs to be removed. The seams left from casting are ground down and the piece is then filed by hand with respect for the shape and design of each model.
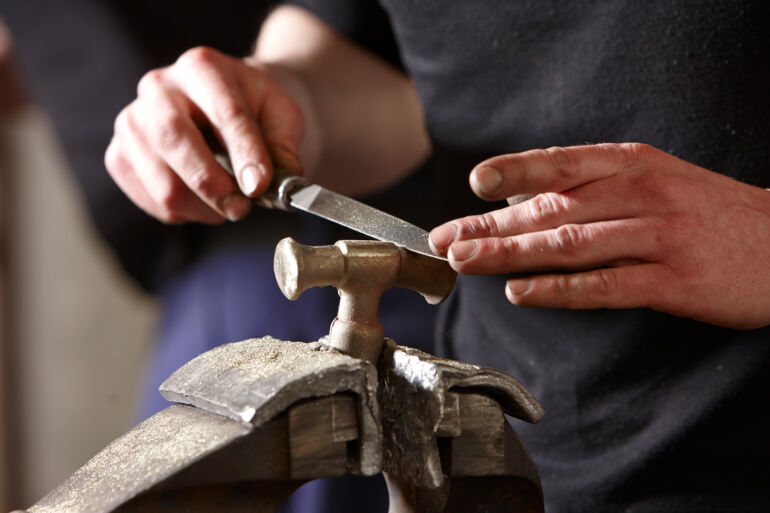
Hand Turning
Round pieces will not be filed, but turned by hand to remove the crust from the casting and to re-accentuate the lines and shapes.
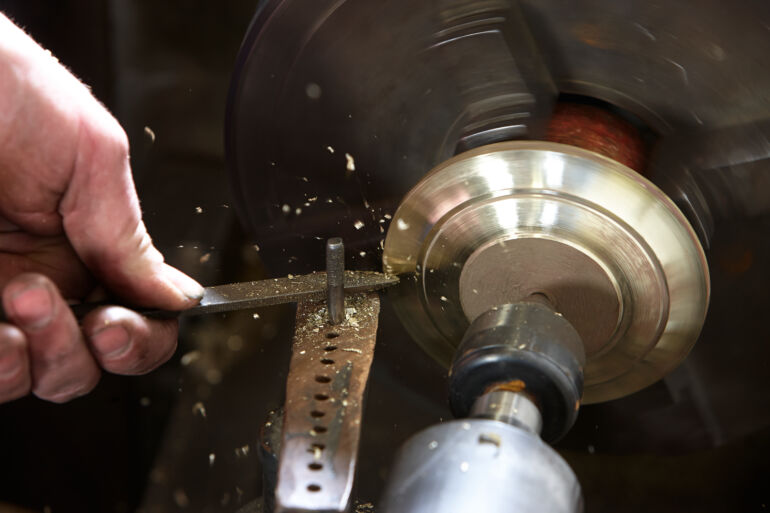
Chiseling
The chiseler uses an arsenal of custom made tools, pearlers, tracers, embossers and 'rifloirs' in order to make thousands knocks and strikes a day; each movement animates gradually the shapes out of the 'spongy' brass texture. The piece comes to life. Here an Acanthus leaf, there the scales of a snake.
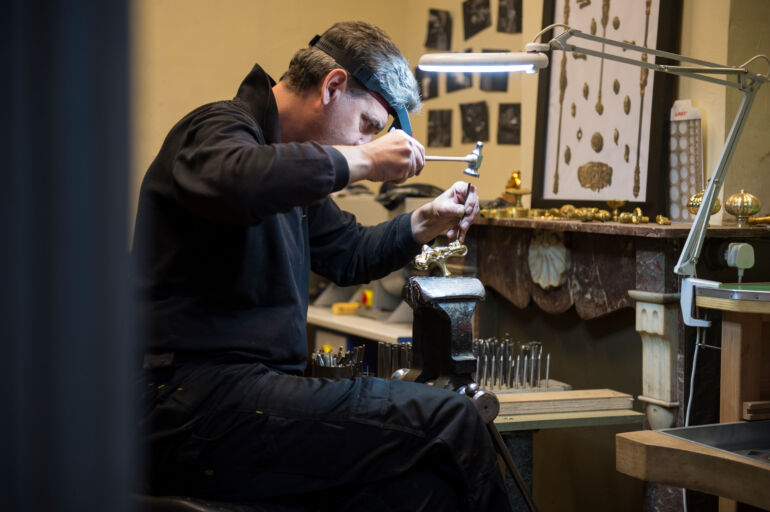
Chasing on Pitch
The Pitch is a bowl filled with a special compound called 'le ciment' in French in which the piece is captured. This procedure allows the chiseler to rotate the piece in every position with an immense freedom without damaging the jewel in the making.
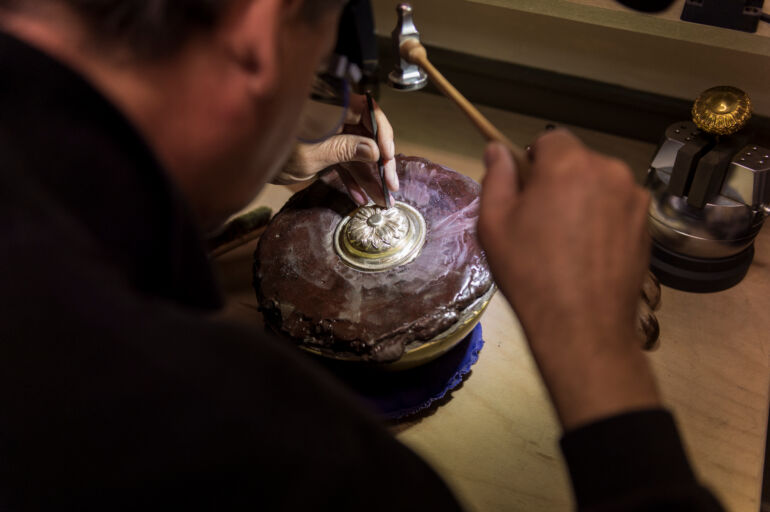
Brushing, Wiring, Polishing
Different steps are necessary before a filed or turned piece obtains its delicate polished or brushed texture. Brushing with horse bristles, cloth bristles - each step involves using the right compound, the right movement without losing the detail and expression of each piece.
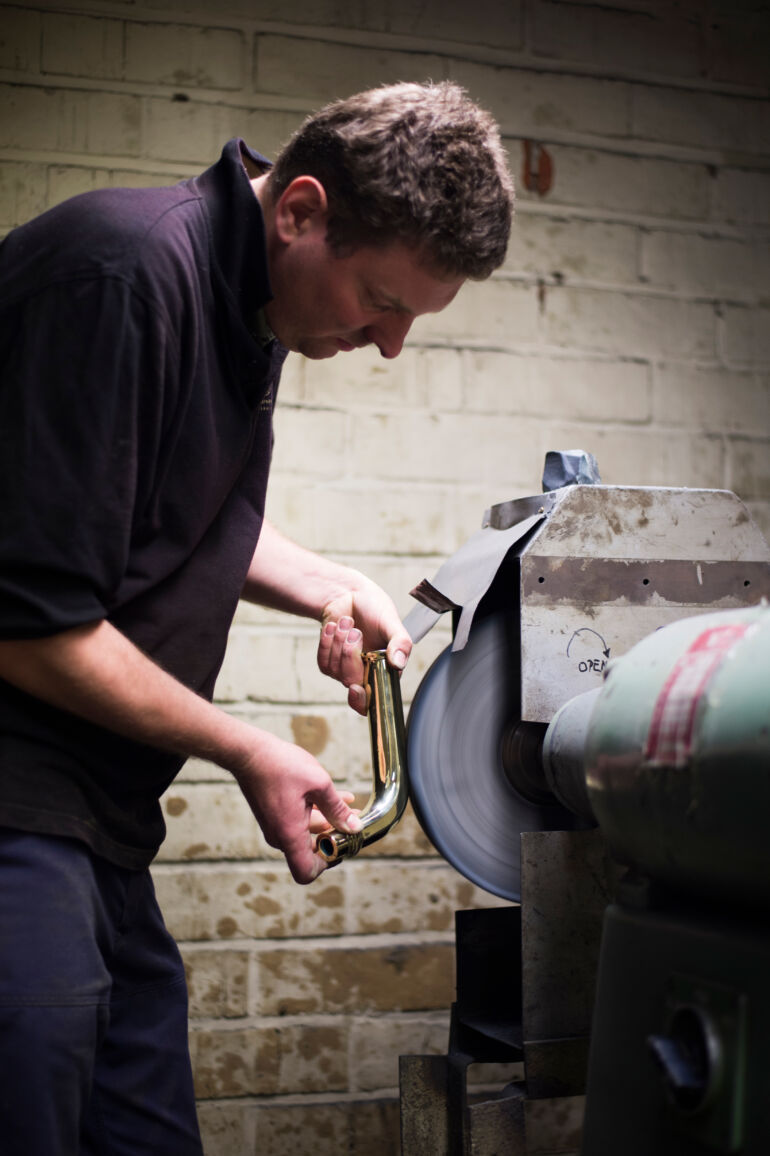
Hot Forging
While brass is reworked cold, forging iron means heating up the piece and blowing it with a hammer on an anvil while it's hot until it gets the desired shape and function. The picture shows a Moustache Hinge in the making.
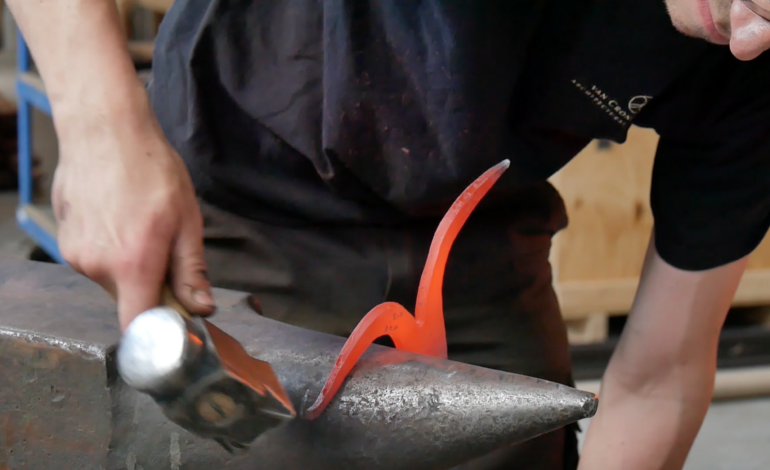
Bronzing
van Cronenburg is famous for the authenticity and depth it creates with its finishes. Obtained by an in-house labor-intensive process, they give each piece a unique character.
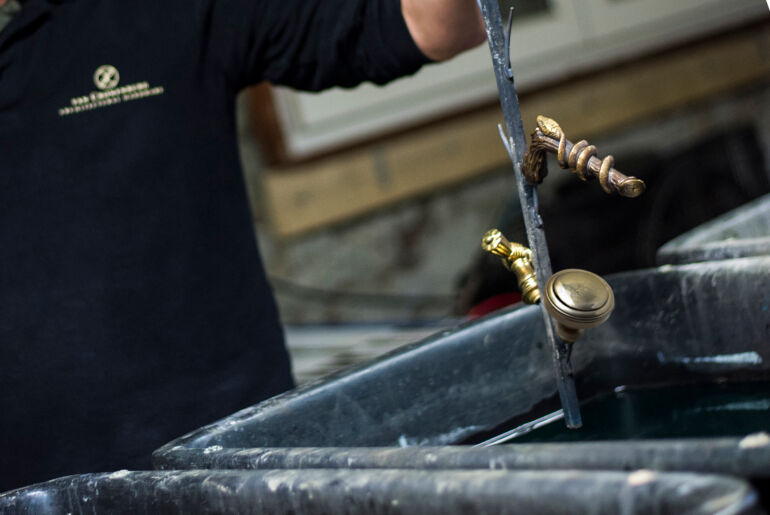